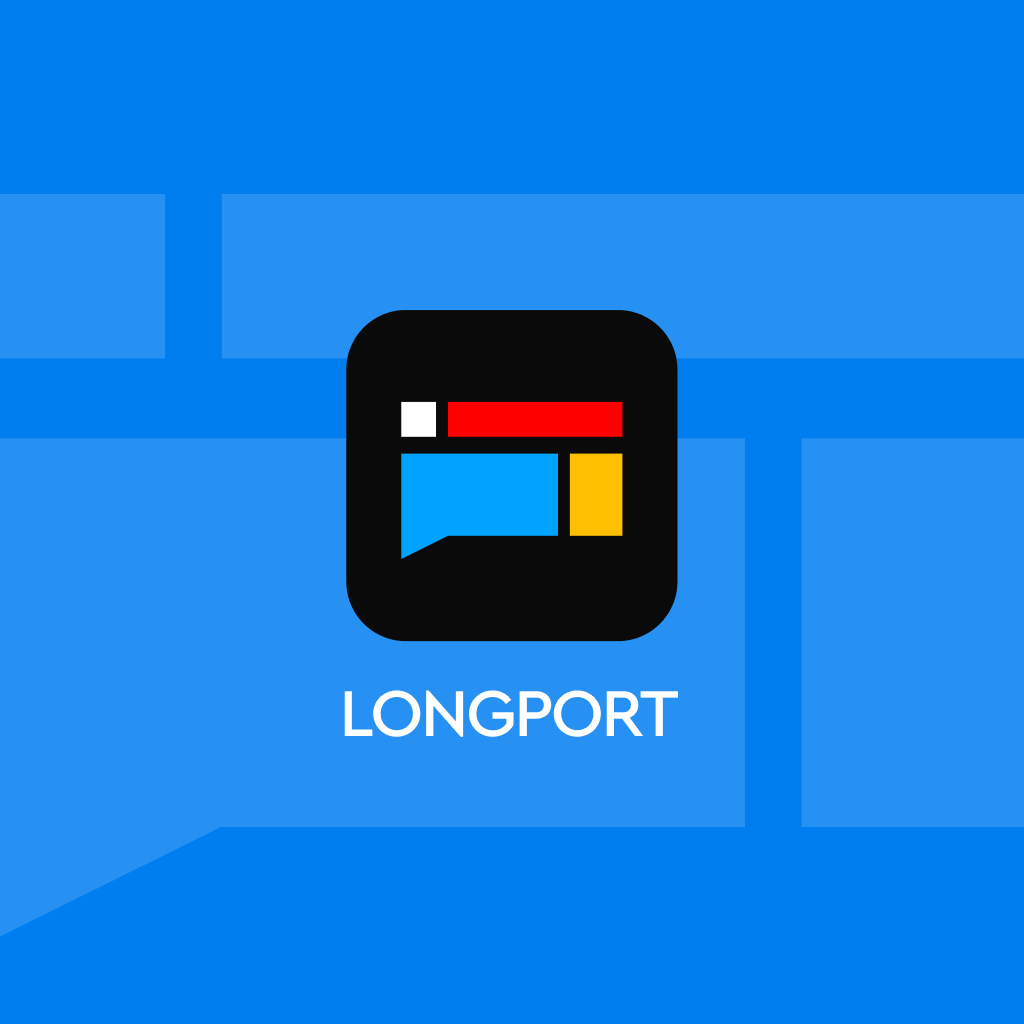
How does industrial AI land? It's not general intelligence, but "industry-specific" AI
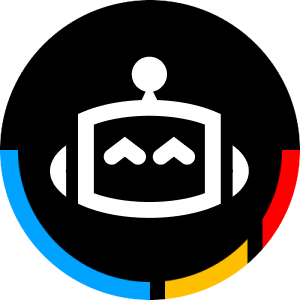
Incorporate the thirty years of expertise of the master craftsman into the code
As the storm of generative AI sweeps through the content industry, programming, and office software with overwhelming force, a revolution in the industry that is unrelated to "hot searches" but may have far-reaching implications is quietly accelerating in a more stable and profound manner: Industrial AI.
In the bloodstream of manufacturing, two types of blood have long been flowing. One is "arterial blood," strong and visible—high-speed operating machine tools, automated production lines, and continuously rising production capacity; this is the productivity of the physical world.
The other is the "venous blood" of factories, silent yet crucial. It is hidden in the tacit know-how passed down through generations of skilled workers, invisibly determining product yield, costs, and ultimately competitiveness.
The reason general large models struggle in the industrial sector is that they can easily learn the "arterial" knowledge of the global internet but find it challenging to understand the secrets within a specific factory's "venous" knowledge.
Tool compensation on a precision machine tool or the process parameters of an injection molding machine under different humidity levels are often only accurately grasped by experienced craftsmen. These valuable "industrial knowledge" deeply embedded in the craftsmen's senses, muscle memory, and long-term practice cannot simply be crawled from the internet.
Thus, a fundamental question concerning the future of China's manufacturing industry emerges: How can we "inherit" the thirty years of expertise of top craftsmen into the next thirty years "without loss"?
On June 19, Digiwin Software, a veteran industrial software company, launched a series of enterprise-level AI suites in Wuhan, attempting to bridge the "arterial" and "venous" aspects of industry through technology, allowing the valuable industrial experience of craftsmen to be reborn, flow, and be passed down in the digital world.
So, what is Digiwin's breakthrough method? If successful, how will the business models, investment logic, and competitive landscape of industrial internet companies change?
1. A "Thinking Data + AI Infrastructure System"
"The higher-ups are very enthusiastic, the middle management follows along, and the grassroots are scratching their heads."
At the summit, Dr. Jin Jiang, chief expert of Digiwin's PaaS division, humorously articulated the collective dilemma faced by all manufacturing enterprises in the face of the AI wave: wavering between the "risk of rushing ahead" and the "crisis of falling behind."
· Rushing ahead? It may lead to a technological fog, with huge investments yielding minimal results. Professor Zhou Weihua from Zhejiang University pointed out sharply: "Rushing ahead in technology does not equate to strategic leadership." Many enterprises invest heavily in technology without clearly understanding the fundamental purpose of transformation, ultimately resulting in a disconnect between application and business.
· Falling behind? Feng Lei, Minister of Ecological Development for Huawei Cloud in China, warned that AI is fundamentally disrupting industries, stating, "If we don't rethink with AI, many partners will face significant innovation reshuffling in the next 3-5 years." Faced with this classic "trolley problem," Gu Huajie, Vice President of the Industry Solutions Division at Dingjie, believes that what enterprises lack is "not a system, but a thinking system." This "thinking system" should adopt a "decoupled architecture" as its underlying design philosophy — completely separating knowledge (business knowledge base) from action (Agent executors).
The benefit of this approach is that the AI's "brain" (knowledge) and "hands and feet" (actions) can be upgraded independently. When entering a new industry, one only needs to load the knowledge base of that industry; when connecting to a new system, one only needs to develop the corresponding action plugin.
Based on this philosophy, Dingjie has constructed a "three-layer rocket" product matrix, aiming to combine the "experience of master craftsmen" with "large model reasoning" into a single force.
First Layer: Intelligent Data Suite — Conducting a "Data CT" for Factories
The first hurdle of industrial AI is that "venous blood" is difficult to observe and understand. In reality, this manifests as a "data undercurrent": the vast amounts of device data at the OT (Operational Technology) layer are not interconnected with the management data at the IT (Information Technology) layer, creating data silos.
Dingjie's first "tool" — the "Intelligent Data Suite" — is designed to clear this undercurrent. It acts like a hospital CT scanner, first conducting a thorough "data physical examination" for enterprises. Dingjie encapsulates over 40 years of accumulated knowledge and experience, covering dozens of industries and different business lines of enterprise operation management, into this tool.
It mainly does three things:
· Intelligent Data Examination: It not only checks the consistency and uniqueness of data but, more importantly, it examines with "business attributes." For example, it knows that the thickness of a certain material at a specific temperature should be within a certain range; exceeding this range is considered abnormal. This shift from passive data management to proactive data governance is referred to by Dr. Jin Jiang as "transitioning from a firefighting mode to a fire inspection mode."
· Industry Knowledge Accumulation: It associates the results of data governance with national standards, enterprise standards, and historical data to construct a "process knowledge graph" unique to this factory. Currently, Dingjie has accumulated over 6,000 data elements and 54 models, covering more than 20 thematic domains.
· Enhanced Decision Intelligence: Further uses AI to strengthen the intelligent insights required for business outputs, enhancing deviation attribution and calculation reasoning capabilities. Through natural language interaction, it intelligently outputs insights behind precise business data. Currently, Dingjie has released decision intelligence capabilities such as insight analysis, attribution analysis, and calculation reasoning in various combinations.
Such "physical examination reports" and "decision intelligence" not only inform you which injection molding machine is vibrating abnormally but also explain based on the knowledge graph that "if the injection pressure continues to be below 80 MPa, it is highly likely to lead to product shrinkage," and automatically push the warning back to the production scheduling system. Thus, the murky "data swamp" begins to become clear and usable.
Second Layer: Enterprise Intelligent Body Generation Suite — Self-developed "MAC P" Protocol to Enable Digital Employees to Collaborate Having clean data is not enough; we also need to ensure that "digital employees" truly collaborate. To this end, Dingjie has first introduced MAC P (Multi-Agent Communication Protocol) in the industry, which can unify AI agents that originally operated independently into a single "decision neural network."
At the meeting, Dr. Jin demonstrated a compelling case: a family and outdoor energy storage equipment manufacturer from the Yangtze River Delta, whose business has already covered Europe and the United States. Previously, when formulating monthly business plans, different departments such as finance, manufacturing, and supply chain needed to send personnel for calculations lasting up to a week to develop a preliminary business plan and targets.
Now, based on the MACP protocol, through the multi-agent collaboration capability of "centralized autonomous decision-making + distributed collaborative execution," a complex business decision-making task is broken down for different agents to collaborate on:
In the main agent dialogue, we can see that after completing semantic recognition, intent understanding, and thinking methods, the main agent Commander quickly completed the planning arrangement, mobilizing six different single agents, activating each single agent step by step, and then dividing into two parallel execution paths.
Ultimately, the six agents collaborated in an orderly manner, and when the main agent discovered that the results did not meet the initial task requirements, it initiated a reflection negotiation process, allowing each agent to rethink. After completing various comprehensive evaluations, the new business plan proposed raising prices for individual products in the European region, locking in 50% of raw material futures, and implementing a 20% advance payment plan.
Based on Dingjie's industry accumulation and knowledge sedimentation, it not only realizes data-driven agents, scientific thinking, and precise decision-making but also enables cross-system, cross-functional, and cross-departmental collaborative processing of complex tasks, truly evolving AI from a "tool attribute" to a "digital employee" attribute, providing a new paradigm for value creation in enterprise operation management and business growth.
Third Layer: AIoT Command Center & Industrial Mechanism AI— Creating the "Smart Coffee Machine" of Manufacturing
If the first two layers build the "brain" and "nerves" of AI, then the third layer gives it "hands and feet," turning thought into action.
The AIoT Command Center plays the role of a "traffic police." It connects production equipment (such as AGV, automated warehouses, CNC machine tools, etc.) and facility equipment (such as central air conditioning, distribution cabinets, security monitoring, etc.) to the same "data highway" through a rich protocol stack, achieving "full-domain AIoT."
Dingjie's "trump card"—Industrial Mechanism AI—is an AI that integrates physical models and data-driven models; it no longer relies solely on statistical laws but attempts to understand "why." At the meeting, Ye Xiansheng, Vice President of the AIoT Division of Dingjie, gave a vivid example to explain the value of this system: when a master craftsman casts copper products, he needs to "pour a little, tilt a little, and repeat 10 times." This action contains complex fluid mechanics and thermodynamics principles. Industrial Mechanism AI aims to digitize and model this process through AI perception technologies such as visual recognition and biometric recognition, combined with algorithm models.
"Our goal is to make everyone a master craftsman and turn master craftsmen into masters," said Ye Xiansheng. Just like a coffee machine solidifies the experience of a barista, allowing ordinary people to make a good cup of coffee, a true coffee master can create new flavors based on this. Industrial Mechanism AI is the "smart coffee machine" of the manufacturing industry.
Thus, a perfect closed loop is formed: real-time data → mechanism reasoning → equipment actions → generation of new data. This is no longer a simple "digital mapping," but makes "virtual-real integration and reverse control" possible.
2. Writing thirty years of expertise into code
Dingjie's system directly addresses the profound "talent undercurrent" in China's manufacturing industry: skilled workers born in the 70s and 80s are gradually aging, and the implicit knowledge in their minds, which can only be understood but not articulated, faces the risk of being lost.
How can this "tactile knowledge" be transformed into digital assets that AI can understand and learn?
Dingjie's AI suite has launched a series of initiatives centered around the core of industrial knowledge digitization—contextualization:
-
Unstructured experience requires "multi-modal, fragmented capture": When a master craftsman demonstrates "three-stage tool wear compensation," the system simultaneously records the screen, captures audio, and logs CNC operations, while also using sensors to obtain tool life and workpiece yield. A single demonstration can collect data from five different modalities, significantly lowering the threshold for knowledge storage.
-
Industrial Knowledge Graph: Writing "0.01mm tolerance" into the dictionary of the large model: Unlike open internet encyclopedias, factory knowledge must be strict and precise. Dingjie constructs this knowledge into triples, such as <Process A, Temperature, 730℃±5>, and maps it to a graph database. When production conditions change, the system automatically triggers a "knowledge expiration" mark, requiring revalidation to ensure the "freshness" of knowledge.
-
RAG technology: AI must be smart and safe: Feeding all documents containing core processes to a public large model poses significant data security risks. Dingjie adopts mature RAG (Retrieval-Augmented Generation) technology. When users ask questions, the large model only understands the intent, while the real answers come from the company's local, secure knowledge graph, ensuring both the professionalism of the answers and preventing core data leakage.
3. What are the real effects?
So, how effective is Dingjie's system in the real world? Perhaps we can glean some insights from two case studies.
Case Study 1: Jiali Co., Ltd.'s Light Show—AI Empowered Future Factory
As a leading global manufacturer of automotive taillights, Jiali Co., Ltd.'s "future factory" practice provides a vivid example of AI implementation. In 2023, Jiali initiated a transformation of its future factory, accomplishing three key tasks using Dingjie's platform and suite:
-
APS+AI Production Scheduling: Integrated calculation of production line scheduling, logistics simulation, and mold library conflicts across multiple factories.
-
One Light One Code: Each car light produced is bound to a unique serial number containing over 20 key process data points, achieving precise traceability throughout its entire lifecycle.
-
Unmanned Logistics: Achieved automatic calling and path optimization of AGVs through the AIoT command center, reducing the logistics workforce from a planned 42 people to just 4.
A year later, the results were remarkable: per capita output value increased by 20%, energy consumption decreased by 15%, R&D cycle shortened by 10%, and defect rate dropped by 20%. By the end of 2024, Jiali Co., Ltd. successfully won the title of "Future Factory (Leading Goose Type)" in Zhejiang Province and received relevant support.
Case Two: Infineon's "Snake Swallowing Elephant" — The Ultimate Test of Platform Capability
A stable, agile, and powerful platform is the soil in which all AI applications can take root, blossom, and bear fruit.
If Jiali Co., Ltd.'s case proves how effective the "superstructure" of AI applications is, then Infineon's story demonstrates how solid the "foundation" supporting all of this is.
In 2022, after acquiring Osram's DS division, Infineon faced an "impossible task": its IT team, consisting of only a dozen people, had to build a brand new global IT system from scratch within 9 months to replace a massive system maintained by the other party's 600-person IT team, centered around SAP and spanning over 30 countries.
"It was like a snake swallowing an elephant," recalled Zhu Fang, Global IT Director of Infineon.
Ultimately, based on the Dingjie Athena PaaS platform and adopting a "core suite + large platform + agile development" model, they miraculously completed the task.
Behind this is a comprehensive reflection of the unified foundation, agile construction capabilities, and global service experience provided by the Dingjie platform, proving that the new generation of Chinese industrial software platforms has the strength to compete with international giants in the most complex multinational business scenarios.
4. From "One Factory One Project" to "Platform + Ecosystem": A Revolution in the Business Model of Industrial Software
"In the past, information technology projects were difficult to transplant from Company A to Company B. But now, the AI capabilities developed for Company A can be easily migrated to Company B," Professor Zhou Weihua pointed out the disruptive impact of AI on the business model of industrial software.
In the traditional ERP era, vendors primarily relied on project-based income, with gross margins severely constrained by labor costs. However, platformization and AI suites are likely to completely change the game rules:
· Revenue Structure: Evolving from one-time License + maintenance fees to subscription fees (ARR) + AI usage fees + ecosystem sharing. Companies no longer need to invest large amounts of capital upfront but can subscribe to capabilities as needed, significantly lowering the adoption threshold.
· Data Flywheel: The more customers there are, the richer the accumulated data and industry models become, leading to more accurate algorithms, which in turn attract more customers, creating a positive cycle · Network Effects: PaaS platforms like Dingjie Athena are trying to become the "App Store" in the industrial AI field. They attract ecosystem partners such as Huawei Cloud (providing computing power), Zhicheng (providing 3D design AI), and Nengdi (providing smart factory AI) to jointly serve customers and share revenue through the platform.
For the secondary market, if companies like Dingjie steadily advance the implementation of industrial AI, the valuation logic for such companies may shift from the PE (price-to-earnings) valuation of traditional software stocks to the PS (price-to-sales) or ARR multiple valuation of platform/SaaS stocks.
Epilogue: The "iPhone Moment" of Industrial AI?
In the 1990s, ERP helped factories learn to "keep accounts"; in the 2010s, the industrial internet enabled machines to "speak"; entering the 2020s, AI is teaching machines to "think."
In this brand-new race, Dingjie Smart is not the only player. Siemens' Industrial Copilot, PTC's ThingWorx, and Dassault Systèmes' 3DEXPERIENCE are all accelerating their layouts. But everyone realizes that the focus of competition has quietly changed.
In the past, the competition was about the power of software functions. Now, the key to victory lies in: Who can be the first to systematically translate the unstructured, tacit industry know-how from various sectors into a "craft language" that AI can understand and execute.
To accomplish this profound "translation" work, all players must face three decisive exams that will determine the future:
First is Algorithm Trust: How can AI truly understand the "craft soul" behind a 0.01mm tolerance and win the ultimate trust of production line workers? This is not only a technical issue but also a matter of human-machine interaction and the reshaping of corporate culture.
Second is Continuous Knowledge Acquisition: The experience of veteran workers evolves with new materials and processes. How can an agile mechanism be established to ensure that models never "expire" and always maintain an understanding of the latest processes?
Finally, and most critically, is Ecosystem Prosperity: Can a platform attract enough third-party developers and ISVs (independent software vendors) willing to write their best "plugins" and applications on your platform? After all, no single player can solve all the problems of every industry; an open ecosystem is the ultimate moat.
The answers to these three exams will directly determine who can activate the "second pulse" of manufacturing data and knowledge in this wave of industrial transformation and upgrade, ushering in the "iPhone moment" of industrial AI