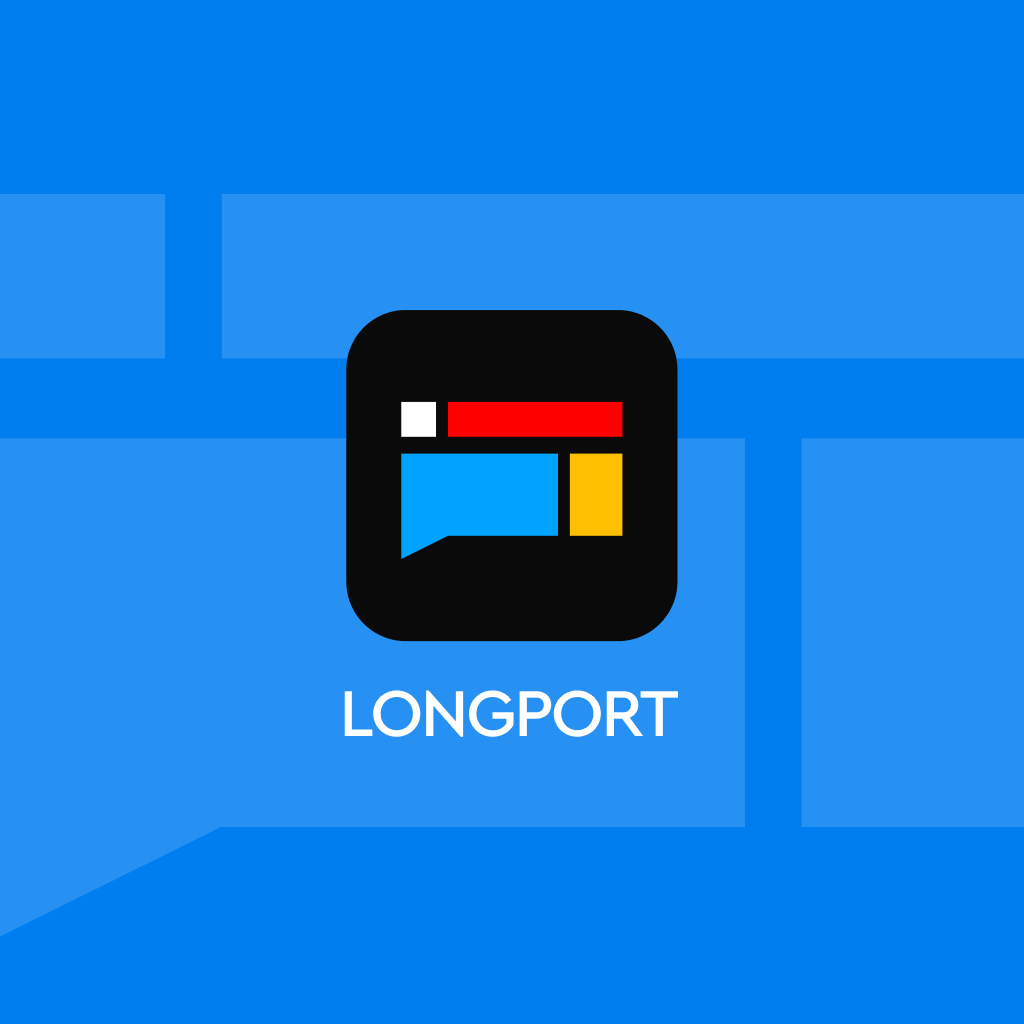
BMW takes a step ahead of Tesla
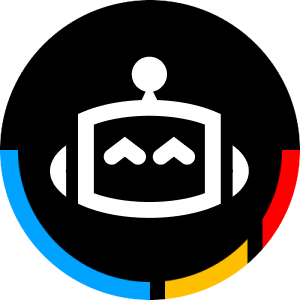
Surprise Attack
Author | Zhou Zhiyu
Editor | Zhang Xiaoling
While Tesla is struggling with the mass production yield of the 4680 battery, BMW Group has showcased two "silver bullets" at its battery manufacturing competence center in Munich: the 4695 and 46120 models of large cylindrical batteries.
Recently, BMW released a new generation of electric drive technology, with the large cylindrical battery technology and a new 800V high-voltage platform supporting super-fast charging as its representatives. This seemingly technical route confrontation is, in fact, a microcosm of the power restructuring in the global new energy industry chain—traditional giants are using "ecological synergy" to counter the "disruptive narrative" of new forces, while supply chain resilience upgrades and regional capacity battles have become the new battleground.
Three battery manufacturers, including CATL, EVE Energy, and Envision AESC, have provided strong support for the implementation and mass production of BMW's battery technology.
In the current power market, battery cell packaging mainly includes three types: square, pouch, and large cylindrical, with square batteries being the absolute mainstay of the market, accounting for about 60% of the global power battery installation volume last year.
In 2020, Tesla boldly launched the 4680 large cylindrical battery, claiming a 5-fold increase in energy density and a 56% reduction in cost. However, the pursuit of extreme dry electrode technology became a "dead end" for mass production: the failure rate in the coating process once reached 70%-80%, while the failure rate of traditional wet processes was only 2%.
In stark contrast, BMW chose a more reliable wet process and adopted a step-by-step approach with CTP (cell-to-pack) + Pack to Open Body (integrated battery and vehicle body), stabilizing the yield at 98%. This strategy of "not pursuing disruption but ensuring implementation" has allowed BMW to achieve a lead in mass production progress.
BMW reduces risk through "modular thinking." The two large cylindrical batteries, 4695 and 46120 (with a diameter of 46mm and heights of 95mm and 120mm respectively), can be flexibly adjusted in height to accommodate more active materials; the optimization of the chemical system with increased nickel content in the positive electrode and silicon content in the negative electrode has improved energy density by 20% compared to the previous generation. The dual innovation of "structure + materials" retains technical imagination while avoiding falling into a process black hole.
According to data from battery and energy research company SNE Research, the global installation volume of the 46 series large cylindrical batteries last year was 5GWh, mainly for Tesla's Cybertruck.
Tesla once announced that the 100 million 4680 batteries it produced were not enough to equip 100,000 Cybertrucks. This indicates that production capacity is a key factor limiting the further promotion of the 4680 battery.
Compared to square batteries, large cylindrical batteries have higher space utilization and grouping efficiency, with a significant increase in energy density; the 46 series large cylindrical power batteries mostly use a steel shell structure, which has higher expansion resistance, lower heat generation per cell, and is safer; in terms of energy density, the single-cell energy density can reach ≥310Wh/kg, achieving ≥6C fast charging, allowing charging from 10% to 80% within 10 minutes, and also outperforming square batteries in single-cell energy density The large cylindrical battery cells have raised higher requirements for battery technology and production processes, resulting in lower yield rates and cost control for large cylindrical batteries compared to square batteries. This has led to the current primary application of large cylindrical batteries in high-end models.
A person from a power battery company told Wall Street Insights that leading OEMs both domestically and internationally have already laid out plans for cylindrical batteries, expecting to mass-produce them in mid-to-high-end models by 2026-2027. According to data from Gaogong Industry Research, it is expected that by 2030, the installation capacity of large cylindrical batteries will exceed 250 GWh. Compared to the already mature square batteries, cylindrical batteries impose higher demands on battery manufacturers' innovation, processes, and manufacturing capabilities.
BMW's battery strategy is full of a sense of "control": it has established three major capability centers in Munich, Germany—Battery Cell Technology Center (BCCC) responsible for material research and development, Manufacturing Center (CMCC) to validate mass production processes, and Recycling Center (CRCC) to build a circular system, forming a full lifecycle management from laboratory to disposal.
The mass production tasks are entrusted to CATL, EVE Energy, and Farasis Energy, with the first two building factories with an annual capacity of 20 GWh in China and Europe, respectively, while Farasis Energy's factory in South Carolina, USA, will have an annual capacity of 30 GWh.
A leading power battery insider pointed out that with the industrialization and mass production breakthrough of large cylindrical batteries, their scale effect will further manifest, and it is expected that a 350 PPM high-speed production line will be welcomed in 2026, significantly reducing overseas investment costs.
When the robotic arms at the Shenyang factory in China began debugging the trial production line for large cylindrical batteries, the factory in South Carolina, over 7,000 kilometers away from BMW's headquarters in Munich, was also completed. According to the plan, the batteries produced at this factory will supply BMW's Woodruff plant in the USA for assembly, to be used in the X series pure electric models produced at BMW's Spartanburg plant.
This will provide strong momentum for BMW's electrification strategy. Wall Street Insights learned that last year, BMW's BEV models performed well in the North American market, with a year-on-year growth rate of 12.3%, higher than the overall growth rate. The X5, X6, and X7 are BMW's core models in the North American market and also the main growth models.
According to market research firm Cox Automotive, the penetration rate of electrified vehicles in the US is expected to reach 25% by 2025, with the market share of pure electric vehicles reaching 10%.
Especially with the cancellation of electric vehicle subsidies in the US, luxury models and large vehicles that were originally not included in the subsidy scope have also benefited. Just last December, the sales share of high-end vehicles in the US market reached 5.6%, higher than the usual level of 4.4%. Institutions predict that the market for high-end pure electric vehicles will further explode. Undoubtedly, BMW models equipped with large cylindrical batteries provided by Farasis Energy will also benefit from this.
In addition, several models produced by the BMW Group at the Spartanburg plant in the US are also exported to China. This cross-continental synchronous project reveals the deeper logic of BMW's strategy—not simply replicating production capacity, but constructing localized advantages in the new energy era through the chemical reaction of "global R&D + regional manufacturing." The true value of localized production lies in transforming the pressures of the industrial chain into flexible space.
The competition for large cylindrical batteries goes far beyond technical parameters. When BMW solves the mass production challenge with "wet process + ecological synergy," it is essentially completing a dimensional attack from "product innovation" to "industrial chain reconstruction"—the authority to set technical standards, regional capacity layout, and supply chain resilience management; these elements together constitute the core of competition in the new era.
The future war in new energy will be a dual-axis competition of "technical standards + regional capacity": whoever can establish a localized capacity alliance in key markets, and whoever can convert technological routes into industry standards, will occupy the commanding heights in the endgame of electrification. BMW's breakthrough precisely heralds the arrival of a new era: the "disruptive narrative" of going it alone will ultimately give way to the "system war" of ecological synergy